Dimensions Ball Mill In Vikram Cement Plant
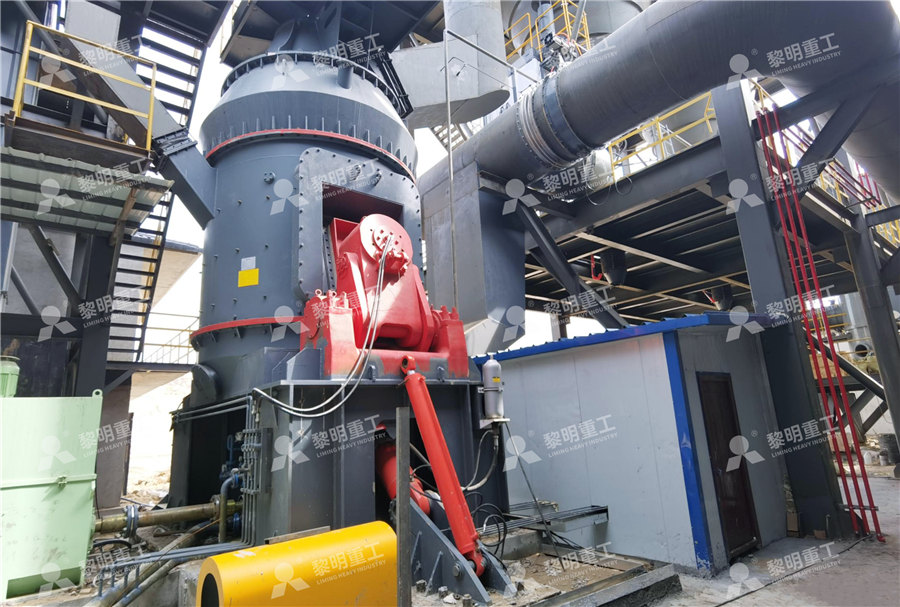
dimensions ball mill in vikram cement plant kooksco
A cement mill (or finish mill in North American usage) is the equipment used to grind the hard, nodular clinker from the cement kiln into the fine grey powder that is cementMost cement is currently ground in ball mills and also vertical roller mills which are more effective than ball mills2021年3月12日 As grinding accounts for a sizeable share in a cement plant’s power consumption, optimisation of grinding equipment such as ball mills can provide significant cost BALL MILLS Ball mill optimisation Holzinger Consulting2023年9月21日 Mill filling level increased by utilizing used segregated media from cement mill(14 MT Charged Grinding Pressure increased from 110 to 125 bar with new rollerUltraTech Cement Limited2017年6月15日 The laboratory ball mill has length 50 cm and diameter 30 cm Grinding media are ceramic and steel balls of 10 mm, 15 mm, 20 mm and 25 mm diameter and density from Design and Optimization of Ball Mill for Clinker Grinding
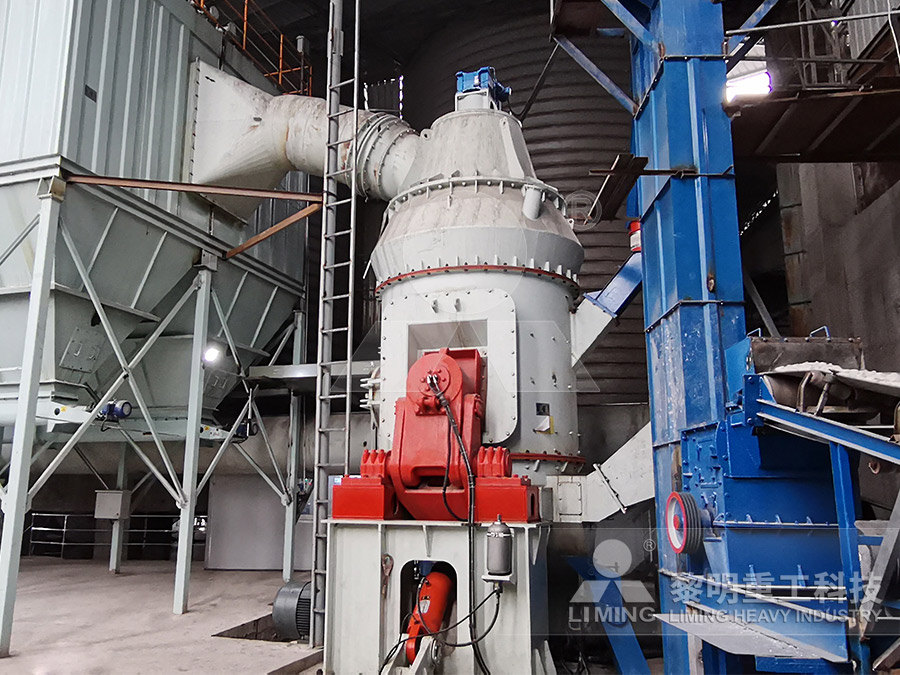
Vikram Cement Neemuch Free Download PDF Ebook
2018年6月3日 • Mechanical transport in place of pneumatic transport from Cement Mill to Cement Silo • Plant capacity enhancement • Water spray at Raw Mill inlet • Expert system for Ball mill is the cement crushing equipment in the cement plant Compared with open circuit ball mill, the closedcircuit ball mill has high efficiency, high output, low cement temperature, and good comprehensive benefit It is the best Ball Mill In Cement Plant Cement Ball MillIn the cement industry, the choice between a vertical roller mill (VRM) and a ball mill for cement grinding is a crucial decision These two types of mills have unique advantages and Vertical roller mill vs ball mill for cement grinding: 2022年11月1日 In numerous cement ball mill operations (Genc, 2008, Tsakalakis and Stamboltzis, 2008, Altun, 2018, Ghalandari and Iranmanesh, 2020), the ratio of maximum ball Impact of ball size distribution, compartment configuration,
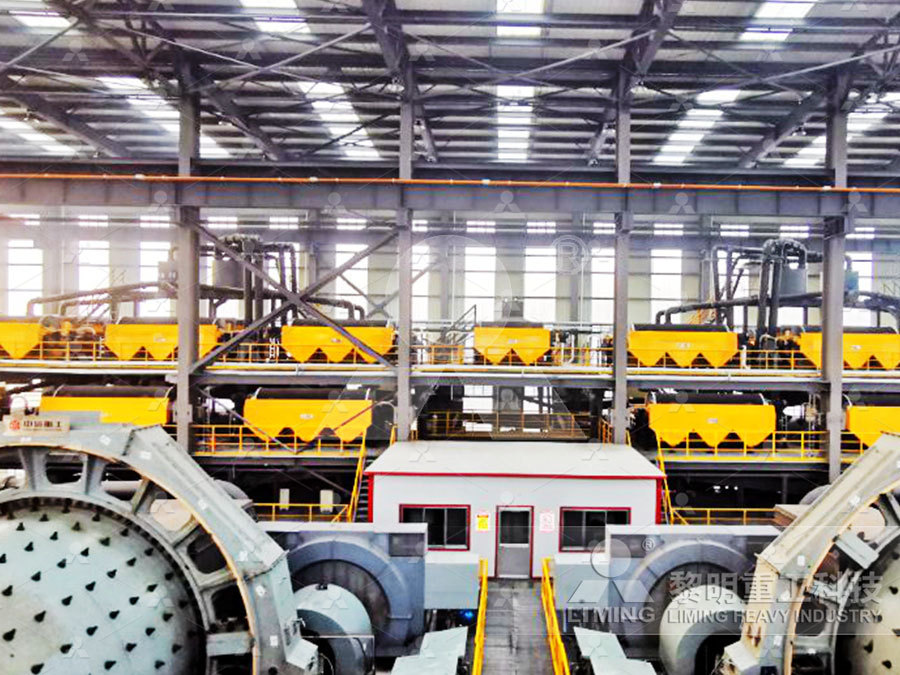
Efficient Ball Mills for Cement Plant Quality
Insmart Ball mills are completely novel kind of mills for high power granulating The unique amalgamation of high friction and collision results in exceptionally fine particles within the shortest amount of time Ball mills are very useful for fine 2020年5月1日 In this work, a cement ball mill (CBM) of a new generation cement plant is considered as a case study in order to study its efficiency based on both first and second laws Energy and exergy analyses for a cement ball mill of a new We supply ball mill balls with various sizes and customization services As a ball mill supplier, our products cover ball mills and related parts, such as ball mill liner, ball mill girth gear, pinion, ball mill diaphragm, etc any need? Our grinding Grinding Ball Ball Mill Balls For Sale Ball Mill Vertical raw mill is one kind of raw mill, generally used to grind bulk, granular, and powder raw materials into required cement raw meal in the cement manufacturing plantVertical raw mill is an ideal grinding mill that crushing, drying, grinding, Vertical Raw Mill Cement Raw Mill Raw Mill In
.jpg)
Performance Evaluation of Vertical Roller Mill in Cement
2024年1月3日 concluded that vertical roller mill circuit has an advantage over conventional ball milling circuit in terms of energy consumption Keywords: Vertical roller mill, cement grinding, performance Cement ball mill and related ball mill system In the real cement project, the production capacity of a cement ball mill can reach 150th200t/h the grinding process of cement transmit relevant energy of cylinder rotation to the lining plate, and then lift and fall, fully mix and grind the materials in the ball mill The liner of the ball mill How To Select Cement Mill? Cement Ball Mill, Vertical Cement Plant2012年6月1日 on mill dimensions, the type of the mill (overflow or grate discharge), the speed of Mill – Cement and Concrete Research, V ol 33, 2003, 439445 16 Ball mills can grind a wide range (PDF) Grinding in Ball Mills: Modeling and Process Control2020年11月22日 Wear Resistance Improvement for Grinding Balls of Horizontal Cement Mill in Cement Plant by NanoCoating Technique (G9917) [12], with dimensions of (d=40mm, t=10mm), as shown in figure (4 Wear Resistance Improvement for Grinding Balls of Horizontal Cement
.jpg)
Cement Plant Machinery Manufacturers, Ball Mill
2021年12月16日 At Supertech, our vision is to integrate our solutions according to our Customers’ needs And keeping this in mind, we manufacture and supply a varied range of Cement Plant Machinery for our Clients and have become a complete solution provider Supertech has successfully emerged as a single stop for all kind of Cement plant machinery The most used coal mills in cement plants are airswept ball mills and vertical roller mills At present, most cement plants use coal as the main fuel in the clinker production process The standard coal consumed by the new dry process for producing 1 ton of cement clinker is usually between 100 kg and 130 kg, and the fuel cost accounts for Coal Mill in Cement Plant Vertical Roller Mill AirSwept Ball MillMills of varied capacity 2 kg, 5 kg 10 kg are available with recommended quantity of grinding media of assorted balls sizes Provision exists for both wet/dry grinding as a cooling jacket is provided The mill’s horizontal rotations enable the High CarbonHigh Chrome balls of different sizes bombard the sample as the mill rotatesEfficient Ball Mills for Cement Plant Quality Control insmart leader in mini cement plant solution As a professional mini cement plant manufacturer with rich experience and own factory, AGICO CEMENT can provide specific cement plant project paper covering all aspects, from market analysis, identifying all items like plant and cement equipment, and raw material to forecasting the financial requirements, etc Based on your real needs, we Mini Cement Plant, Small Cement Plant 100700tpd EPC Cement Plant
.jpg)
8 Tips For Cement Plant Design
2023年11月1日 The design of the raw material grinding system should focus on the energysaving, vertical mill grinding system because of its powersaving, simple process to become a large cement plant, the use of a ball mill grinding 2021年6月29日 The rotating mill is filled with different steel balls of sizes 25 mm, 40mm, 50mm, 60 mm, 70mm and 80 mm with 45%, 40% and ball mills are widely used in cement plants to grind clinker and Effects of Mill Speed and Air Classifier Speed on 2020年11月5日 As you all know, the process of a cement manufacturing plant can be divided into several steps, including crushing, raw milling, clinker calcining, cement milling (or cement grinding), packing and etc In the complete cement 3 Necessary Cement Milling Comparison Ball The cement roller press, also known as roller press in cement plant, high pressure grinding roll (HPGR), is a kind of cement equipment for brittle materials, apply for grinding cement clinker, cement raw material, gypsum, coal, quartz sand, iron ore, blast furnace slag, and other materials The cement roller press is generally applied to the cement grinding plant, according to the real Cement Roller Press, Roller Press In Cement Plant HPGR
G[R.jpg)
Cement Mill Cement Ball Mill Vertical Cement Mill Cement Plant
Wide product range: For meeting various requirements from different clients, our cement mill range from cement ball mill, vertical cement mill, Raymond mill, coal mill in cement plant, etc Strong production ability : AGICO CEMENT has a large production capacity and rich experience to produce any cement equipment required in cement plantBall mills in cement plants have a wide range of applications, including: Grinding of raw materials: The primary function of a ball mill in a cement plant is to grind the raw materials used in the production of cement These raw materials typically include limestone, clay, iron ore, and sometimes sandBall Mill In Cement Plant Selling Various Types Of Cement Mill2021年1月1日 In the study the advantages of vertical roller mill are discussed over ball mills VRM construction, its process and parameters which affects the performance and productivity of vertical roller mill are discussed There are 210 large cement plants having total capacity of 410 MT cement production, with 350 small plants account for the rest Review on vertical roller mill in cement industry its Ball mill disphragm is one part of ball mill liner, it is designed to meet the requirements of partition different sizes of grinding bodies can be separated to prevent them from mixing and interfering with each other material and weight, and your drawings with details, you can send the drawing to s Detailed Ball Mill Diaphragm Cement Ball Mill Diaphragm Cement Plant
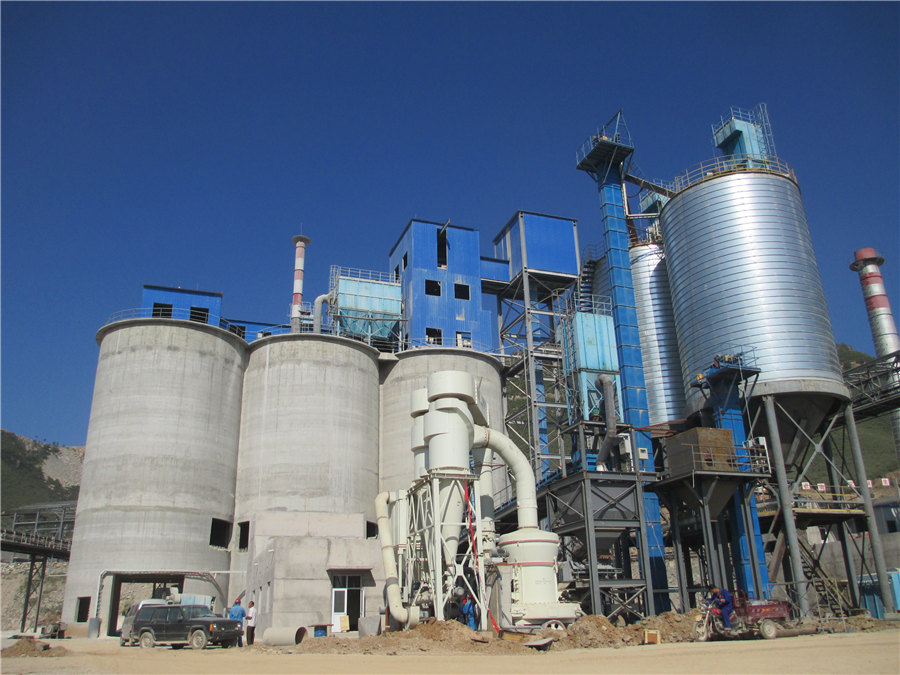
Cement Roller Press Roller Press In Cement Plant Roller
Semifinishing grinding system: after ground by cement roller press, materials are divided into three parts through an air classifier: coarse, medium and fine, in which the coarse material is returned to the roller press for regrinding, the medium material is put into a ball mill for further grinding, and the fine material is directly discharged as the finished cement product2021年3月12日 Ball mill optimisation As grinding accounts for a sizeable share in a cement plant’s power consumption, optimisation of grinding equipment such as ball mills can provide significant cost and CO 2 emission benefits to the cement producer n by Thomas Holzinger, Holzinger Consulting, Switzerland BALL MILLS 1 FEBRUARY 2021 INTERNATIONAL BALL MILLS Ball mill optimisation Holzinger ConsultingCement conveyor refers to a belt conveyor in cement plant, which is necessary accessory equipment in the cement production line A belt conveyor is a kind of material handling equipment with strong adaptability, applied for conveying Cement Conveyor Belt Conveyor In Cement 2017年9月11日 A conventional cement grinding circuit is composed of a two compartment tube mill, a mill filter which collects the fine material inside the mill and a dynamic air separator where final product (PDF) Performance Evaluation of Vertical Roller
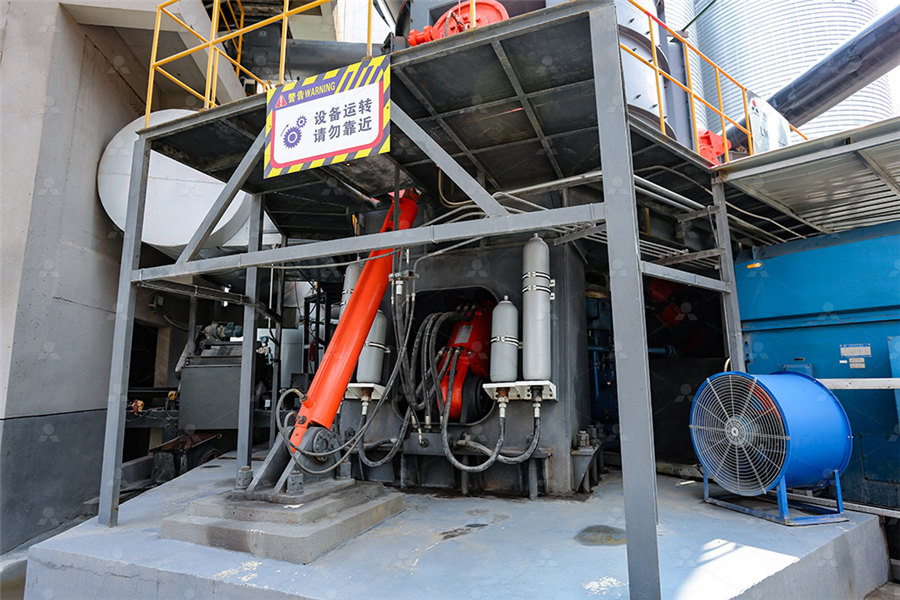
dimensions ball mill in vikram cement plant kooksco
VRM vs Ball Mill for Cement Grinding Page 1 of 1 Feb 10, 2016 VRM vs Ball Mill for Cement Grinding Good Days! Gentlemen, We are planning to put up a new cement grinding plant using Vertical Roller Mill(300350 – TPH) and before implementing the project, we would like to What are the Benefits of a Raw Mill in a Cement Plant? Raw mills play a critical role in cement manufacturing Here are some benefits of using a raw mill in a cement plant: Consistent raw mix quality: Raw mills produce a consistent and homogenous raw What does a Raw Mill do in Cement Plant? ball mills supplierNowadays, ball mills are widely used in cement plants to grind clinker and gypsum to produce cement The research focuses on the mill speed as well as air classifier speed effect on the two a) Cement ball mill view, b) Cement mill sketchThe installation of liners Length Diameter Ratio The lengthdiameter ratio of the cement ball mill is relatively large For mills of opencircuit grinding system, the lengthdiameter ratio is usually between 35 and 6 to ensure that the product fineness is qualified through single grinding; For ball mills in closedcircuit grind system, in order to increase the material flow rate, the length Cement Ball Mill Cost Effective Cement Grinding AGICO Cement Plant
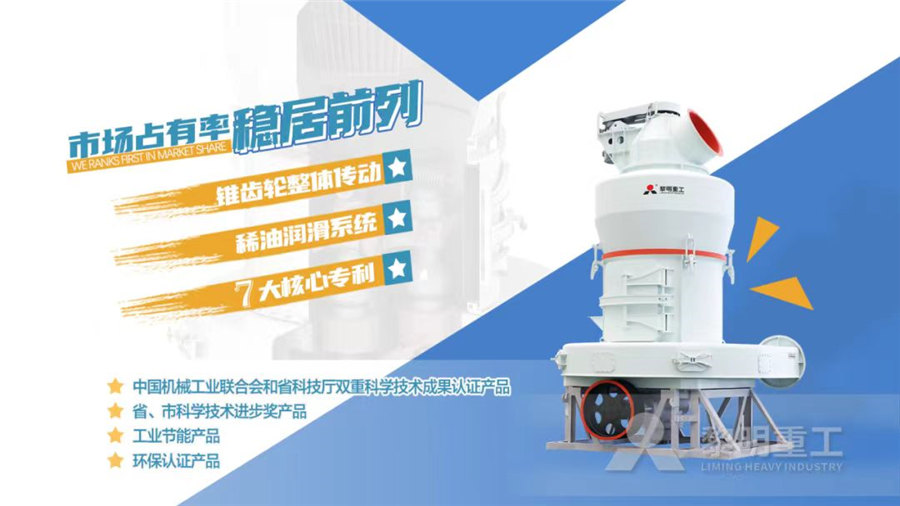
Coal Mill In Cement Plant, Airswept Coal Mill Coal Mill
Airswept coal mill is the main equipment of cement plant, also called coal mill in cement plant, used for grinding and drying various hardness of coal, crushing the coal briquette into pulverized coalIt is the important auxiliary equipment of pulverized coal furnace The airswept coal mill runs reliably, can work continuously, also has a large production capacity and less energy 2021年6月10日 the mill partitions, feed rate, the hardness of the feed material, and ball sizes in the mill Also, using the study done in two similar cement ball mills in the same cement plant, almost (PDF) Ventilation Prediction for an Industrial Cement Raw Ball Mill 2013年8月3日 In Grinding, selecting (calculate) the correct or optimum ball size that allows for the best and optimum/ideal or target grind size to be achieved by your ball mill is an important thing for a Mineral Processing Engineer AKA Calculate and Select Ball Mill Ball Size for The ball mill trunnion, also known as the hollow shaft is an important part of the ball mill that carries the rotation of the ball mill barrel It is a special type of steel casting It mainly plays the role of supporting and connecting the cylinder in Ball Mill Trunnion Hollow Shaft For Ball Mill
.jpg)
Vertical Cement Mill, Vertical Roller Mill Buy Cement Cement Plant
The vertical cement mill is largescale cement grinding machine With advantages of energyefficient and stable quality, vertical roller mill is widely applied to many industries, such as cement, power, metallurgy, chemical and nonmetallic mining industry and etc As a typical type of Cement Mill, vertical cement mill set crushing, drying, grinding, grading transportation in one, it grind The choice between a vertical roller mill and a ball mill for cement grinding ultimately depends on the specific needs and constraints of the cement plant VRMs offer significant energy savings, finer product control, and reduced maintenance costs, making them an attractive option for modern cement plants focused on efficiency and sustainabilityVertical roller mill vs ball mill for cement grinding: 2020年5月1日 Nowadays, ball mills are used widely in cement plants to grind clinker and gypsum to produce cement In this work, the energy and exergy analyses of a cement ball mill (CBM) were performed and some measurements were carried out in an existing CBM in a cement plant to improve the efficiency of the grinding processEnergy and exergy analyses for a cement ball mill of a new Download scientific diagram Schematic of ball mill circuit in the Ilam cement plant from publication: Ventilation Prediction for an Industrial Cement Raw Ball Mill by BNN—A “Conscious Lab Schematic of ball mill circuit in the Ilam cement plant
.jpg)
Optimizing Electrical Energy Consumption In Cement
2023年8月29日 Comminution Optimisation of operating parameters for ball mill In cement plant about 75% electric power is consumed by comminution equipment such as crushers and ball mills and theoretically only 2% of the whole power is used by comminution, the rest being wasted as heat and noise2022年11月1日 In numerous cement ball mill operations (Genc, 2008, Tsakalakis and Stamboltzis, 2008, Altun, 2018, Ghalandari and Iranmanesh, 2020), the ratio of maximum ball size to minimum ball size for coarse milling compartments lies between 13 and 20, while a wider range has been indicated for the fine milling compartments In most of the cases, we Impact of ball size distribution, compartment configuration, Find here Cement Plant manufacturers OEM manufacturers in India Get Contact details address of companies manufacturing and supplying Cement Plant across India Cement Manufacturing Plant, Size/dimension: 24m Diameter, ₹ 1,00,00,000/ Piece; Highquality mining machinery steel ball mill linerpiyali e Automatic cement plant Cement Plant Manufacturers Suppliers in India India